Why Rivet Nuts?
Leave a CommentRivet nuts are becoming more and more popular every year. We would know – we manufacture them.
Their ease of use, high shear and tension strength, and lightning fast installation times are upgrades over traditional bolt and nut, and weld nut applications.
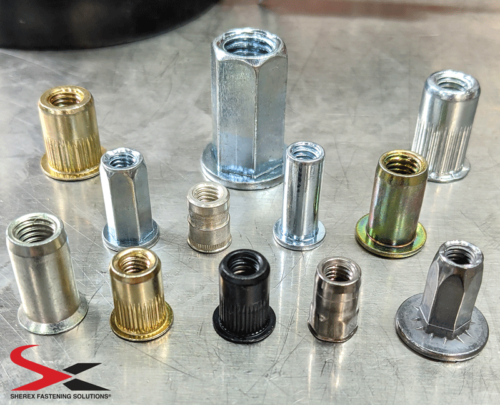
Rivet Nuts come in a variety of styles

Installed Rivet Nuts
A main strength of rivet nuts are that, just like with traditional rivets, they are blind. Meaning, these fasteners can be installed securely from one side of the work piece. No need to struggle to reach around the back of the bolt to fasten the material with a nut. Once the rivet nut is installed, fasten your material through the rivet nut with any compatible externally threaded fastener and you’re all set.
The rivet nut itself can be installed into a variety of a different materials including metal, plastic, fiberglass and carbon fiber. It is used in a wide array of applications in the automotive, heavy truck, and manufacturing industries as they move toward making their products both lightweight and easier to make. In your vehicle, there are likely dozens of rivet nuts for all of the reasons stated above. Lots of them are probably from Sherex!
So how does it work? Installing the rivet nut is easy. Using a hand tool, pneumatic tool, or hydro-neumatic rivet nut tool, place the rivet through a pre-drilled hole. The tool will then crimp the counter-bored section of the rivet nut into the into the back of the installation piece as shown in the .gif below. This leaves the head of the rivet nut laying on top of the material, and the crimped section behind it acting as the nut. That’s really it! In a manufacturing plant, installation can be done through rivet nut automation systems.
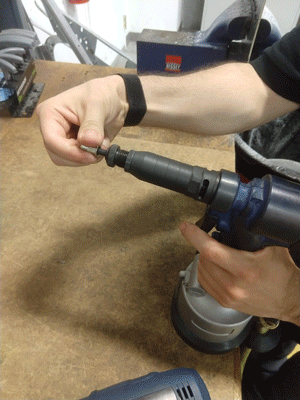
Installing a rivet nut, then attaching to the base material with a bolt
Check out our rivet nut offerings and see the variety of different styles of rivet nuts which we will hit on in upcoming posts. Some applications need a wider grip range to accommodate larger panel thicknesses, some need stronger spin-out or pull-out loads to withstand a variety of expected loads, and some need different finishes, coatings, and other treatments. We will get into all of those topics later!